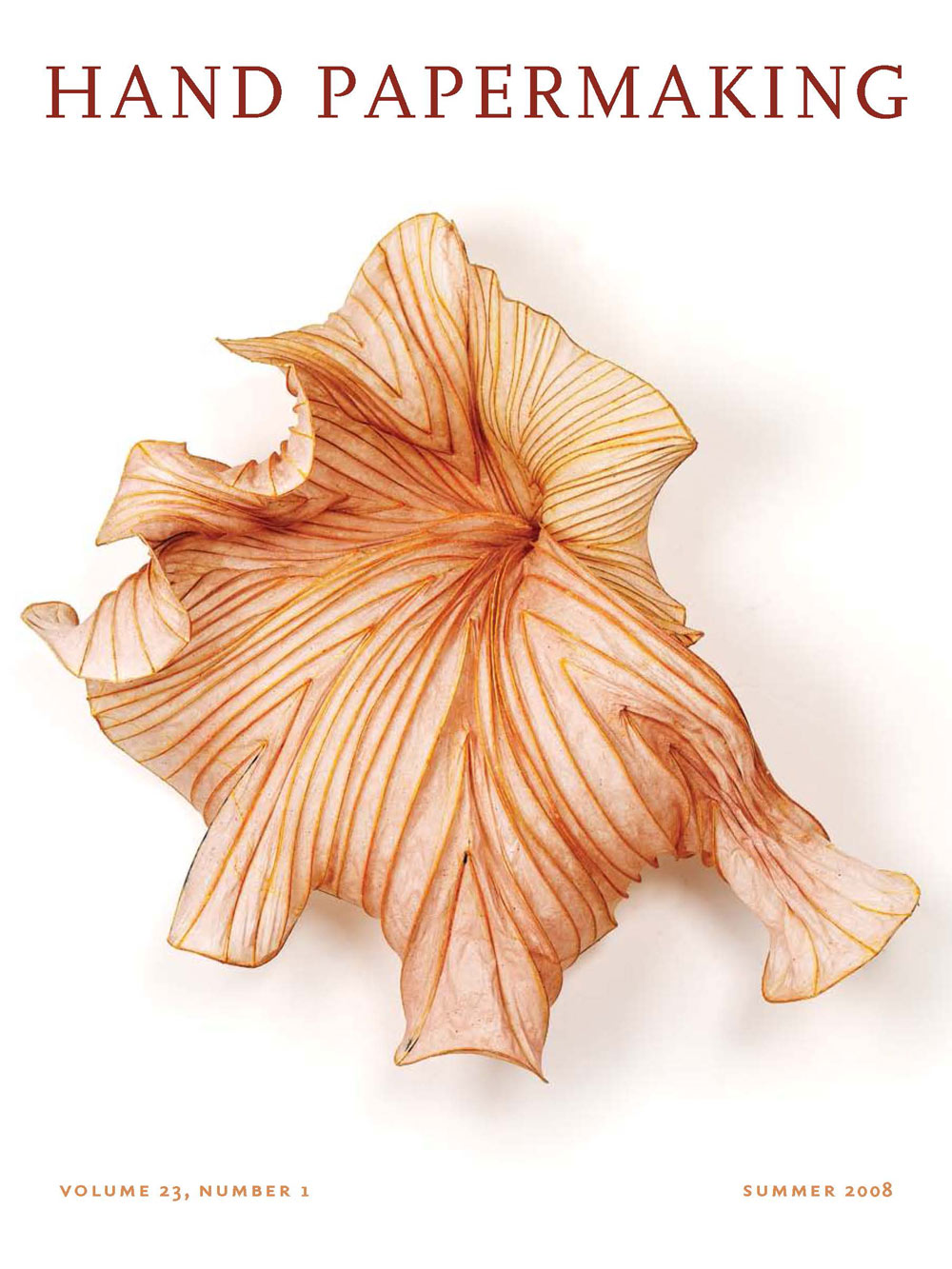
Summer 2008
:
Volume
23
, Number
1
This article begins on page 24 of the Summer 2008 issue of Hand Papermaking
This article begins on page 24 of the Summer 2008 issue of Hand Papermaking
To prepare the pulp for this paper, Sigwald cuts the banano trunk into small pieces using a machete, then cooks the pieces in a very mild caustic solution for an hour and a half. After a cooling period, she rinses the fiber thoroughly and immediately loads it into the Hollander. She beats 3 kilos of fiber to 100 liters of water for 30 minutes. Sigwald forms the sheets Nepalese style on a 2 x 2 meter (78 ¾ x 78 ¾ inch) mould that is an aluminum frame stretched with silkscreen plastic mesh. She removes the moisture with a shop vacuum, running a wide-nozzle attachment against the mesh. After allowing the sheet to rest on the mould for an hour, she peels it off the mould, and places it back on the surface of the mould to dry. While it dries, the paper shrinks, crinkles, and moves in interesting ways. Sometimes Sigwald enhances the crinkling by manipulating the wet sheet. She named the paper Couture because "it moves like an expensive ballgown." Hand Papermaking invited Catherine Nash, the author of "Beater Finesse for the Artist," to curate this issue's offering of paper samples to accompany her article. She selected three handmade papers, created by Betsy Dollar, Margareta Mannervik, and Vicky Sigwald, respectively, for the diversity they represent of fiber choice, beating procedure, sheet forming technique, texture and drape of the paper, and use in the artists' creative work. And geographically they represent a range, with each artist working on a different continent. Hand Papermaking gratefully acknowledges Underwriter-level contributors Ali Fujino, Hiromi Paper International, Charles E. Morgan, Nancy & Mark Tomasko, Beck Whitehead, and Pamela S. Wood, whose generosity sponsored these paper samples. blind print paper sample by Margareta Mannervik, MM Art Paper, Hönö, Sweden This paper is made from 100 percent worn cotton rags. To make the pulp, Mannervik cuts the rags into 3 x 3 cm pieces and slowly feeds half of her beating lot into a Fiber Max Hollander beater with the roll up. After ten minutes she lowers the roll a little. If air bubbles appear on the surface, she adds a few drops of flax oil. After a half hour she loads in the rest of the rags. Every few hours she lowers the roll a bit, never to full contact, and continues to beat until she achieves a pulp that is well macerated, but long fibered (1 to 1 ½ cm long) enough to withstand the pressure of the deep embossment. The pulp for this sample required fifteen hours of beating. The original sheet size is 40 x 40 centimeters, the size used for Mannervik's Blind Print editions. To make the embossed sheets, she forms very thick sheets, leaving them on the mould to drain for several hours before couching. She couches the sheet onto a felt covered with a carrier blanket. Then she places a deeply cut linoleum block upside down onto the wet sheet, covers it with a cotton blanket and a felt on top, and presses each sheet, one at a time, in a hydraulic press. After pressing, she leaves the sheet on its carrier blanket and air dries the sheet, hanging it on a clothesline. atomized opal by Betsy Dollar, Dreampaper Studio, St. Paul, Minnesota, USA This sample is cut from a 4 x 8 foot pulp-sprayed sheet, used by the artist in her installations and large-scale artist books. Dollar prepares her overbeaten unbleached abaca pulp in a Davis Hodges 2-lb. Hollander beater. She loads the beater with the roll fairly high to allow the fiber to circulate and hydrate. She brings the roll down quickly until she hears a grinding sound and lets it run its course for five to six hours. She pigments the pulp and adds enough formation aid—one or two cups per two gallons of pulp—to achieve a consistency of plaster. She sprays the mixture against a stretched muslin frame or insulation foam with a pattern pistol in thin layers. She allows each layer to drain for 45 minutes before applying the next. Two sprayed layers yield a light, translucent paper; three to four layers result in a midweight paper that is strong and transmits light through the dotted spray pattern; and five to six layers give a strong, opaque paper. This sample was made in three layers.